This was the first class in the Unified Robotics Sequence at WPI, and it was very Mechanical-Engineering-heavy. In this class, groups were tasked with designing and building (3D printing) two different four-bar arm and gripper mechanisms that lifted aluminum and 3D-printed PLA plates to various heights and predetermined angles. The two robots were then required to autonomously follow predetermined paths using ultrasonic and reflectance sensors to place and remove the plates from roofs on the field. (See the video at the bottom of the page)
In designing the assembly, I worked on stress calculations related to the gearing selection and arm linkage lengths, torque analysis of the arm motor, the CAD model of the robot, as well as coded (in C++) much of the state machine and encoder interrupts that drove the robot.

Bottom-out Gripper Robot with PLA Plate
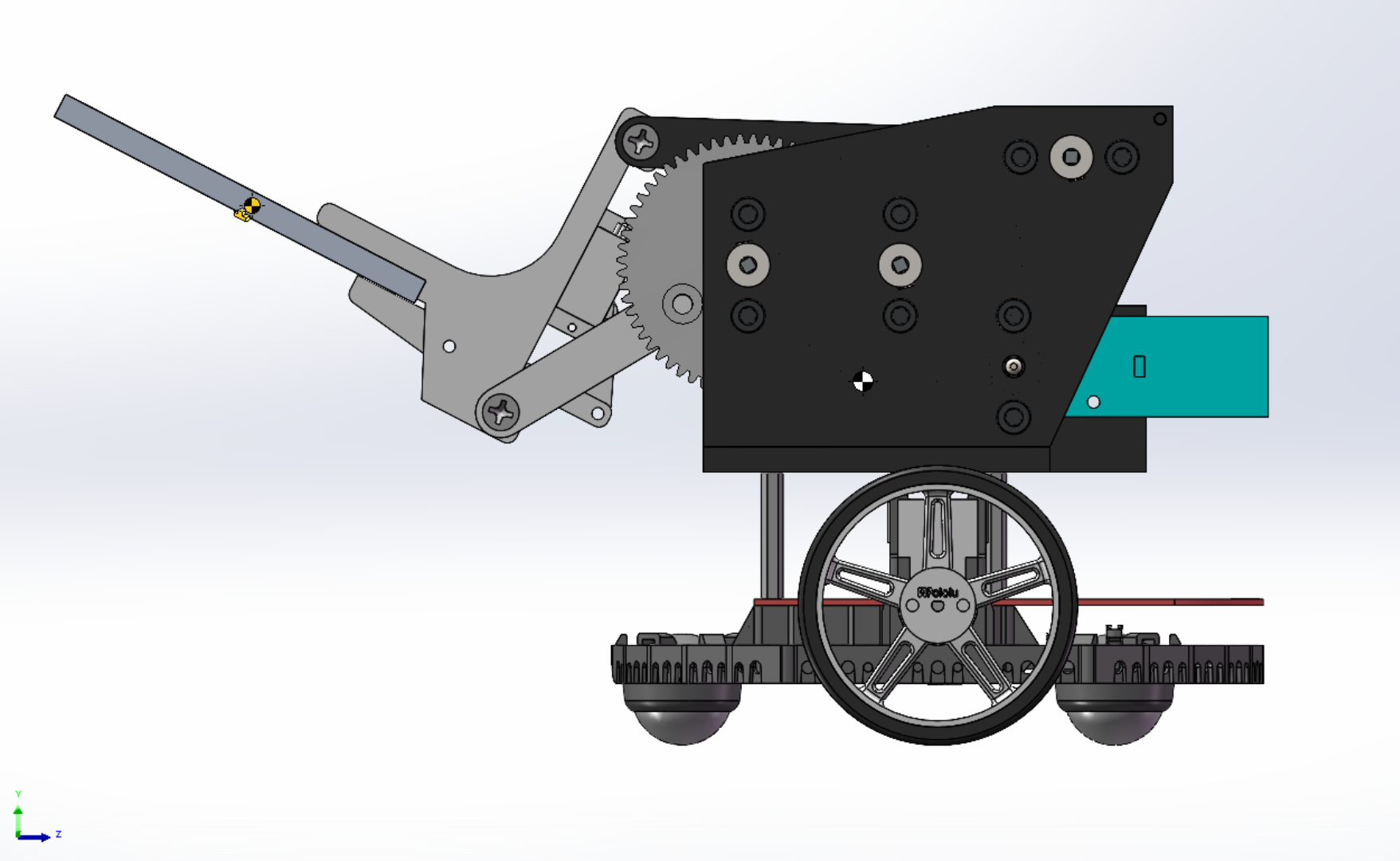
SolidWorks 3D Model of the Bottom out Gripper Robot
Other Photos and Videos of the Two Robots:
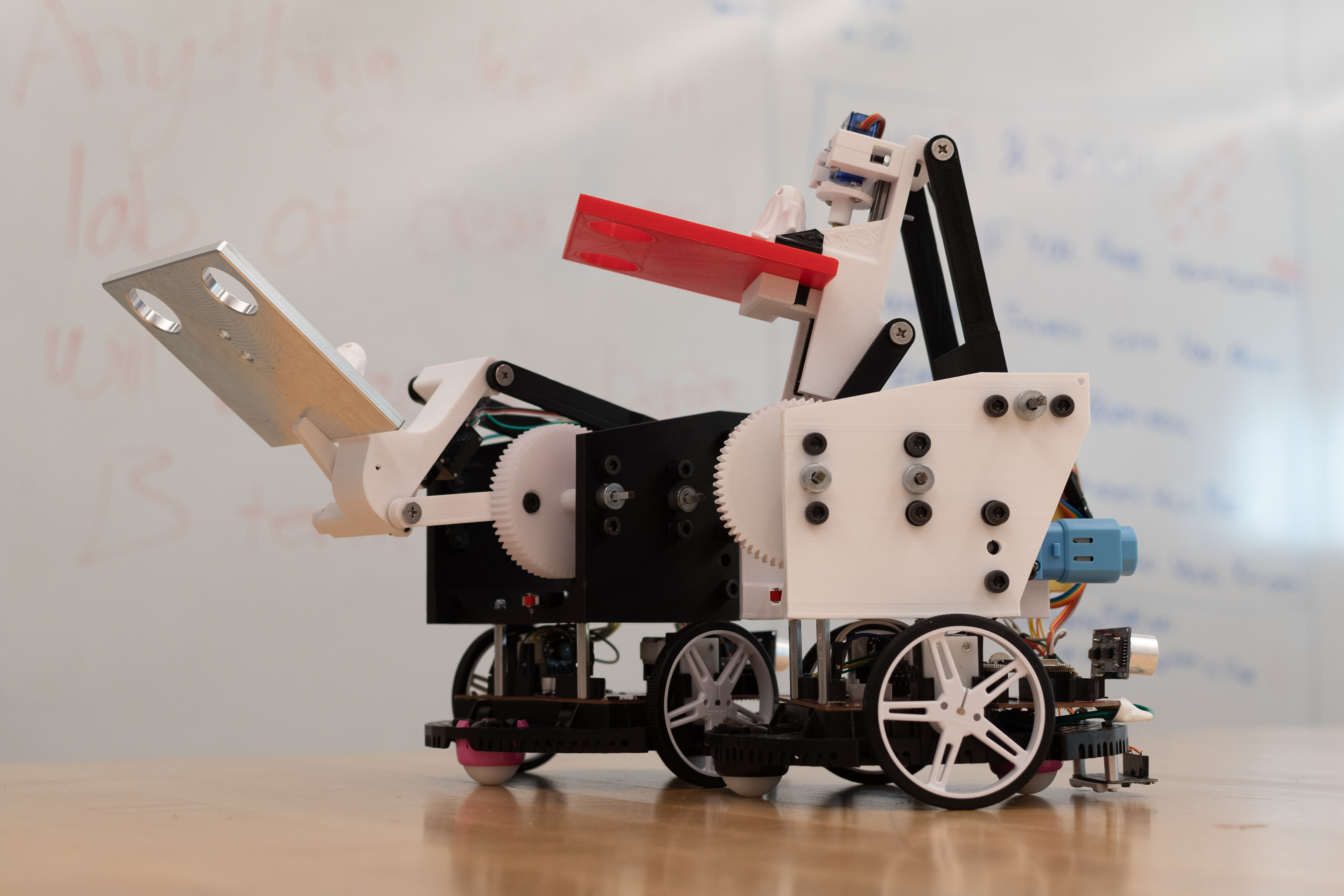
Both Robots with Plates
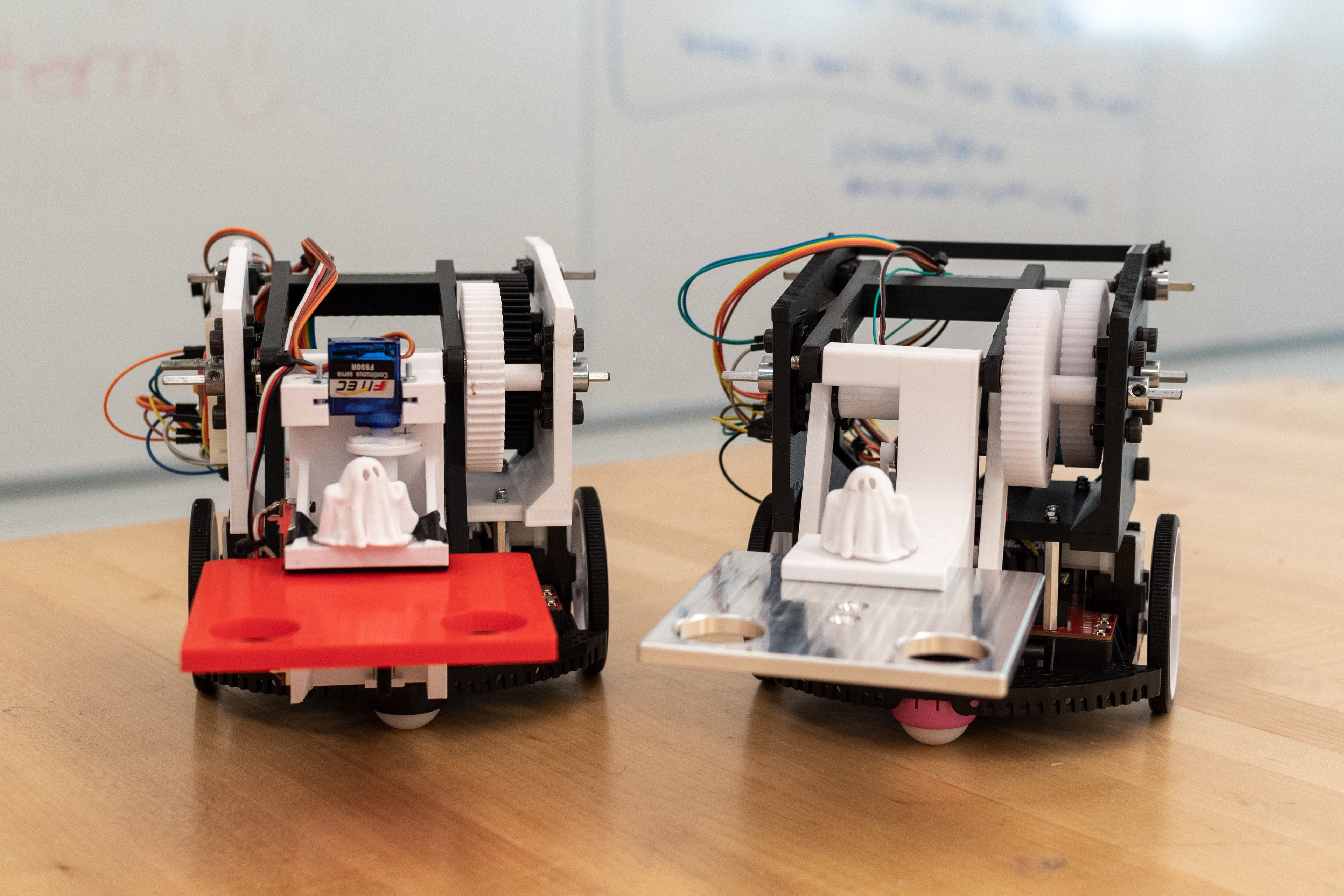
Both Robots with Plates
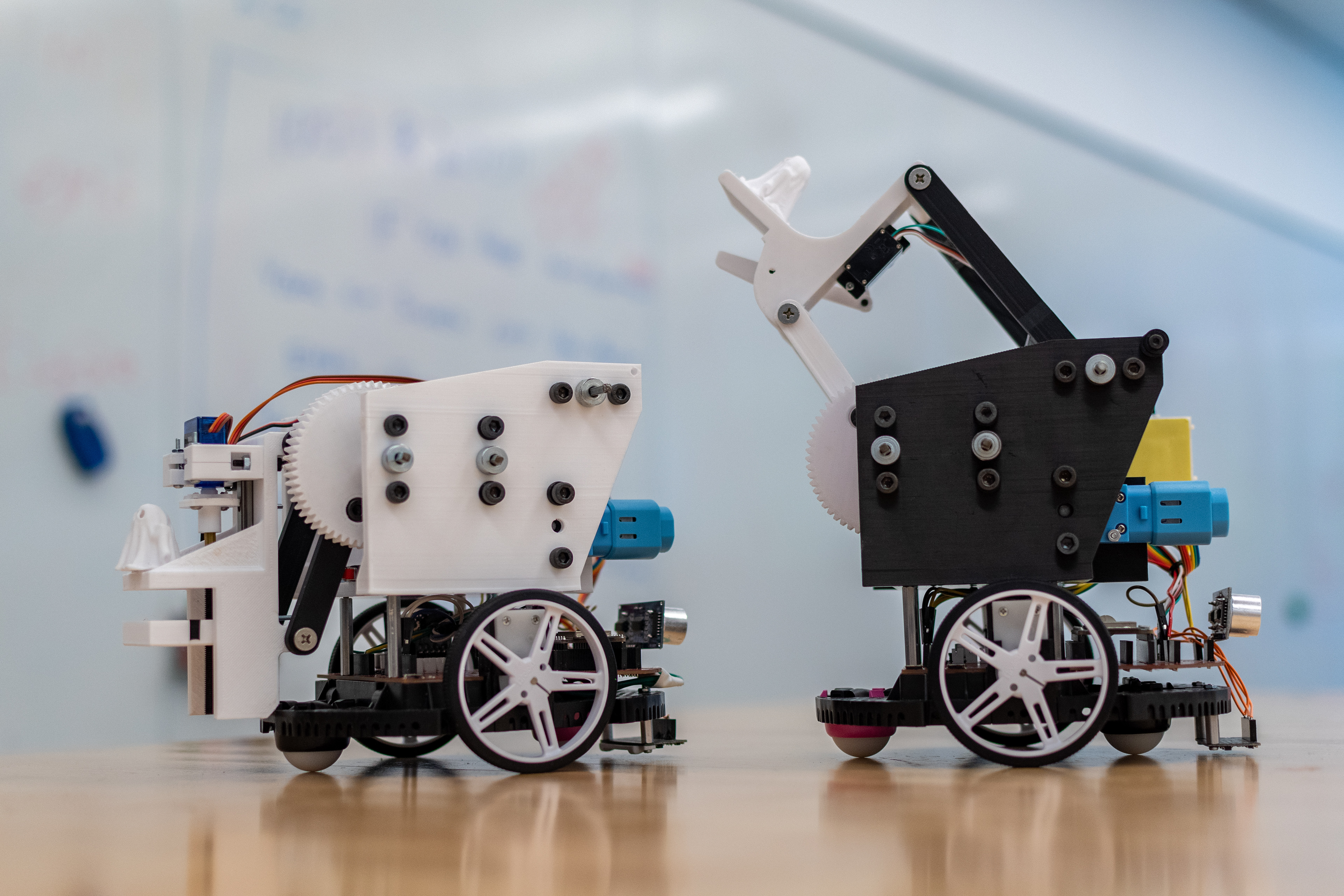
Both Robots With Grippers Open
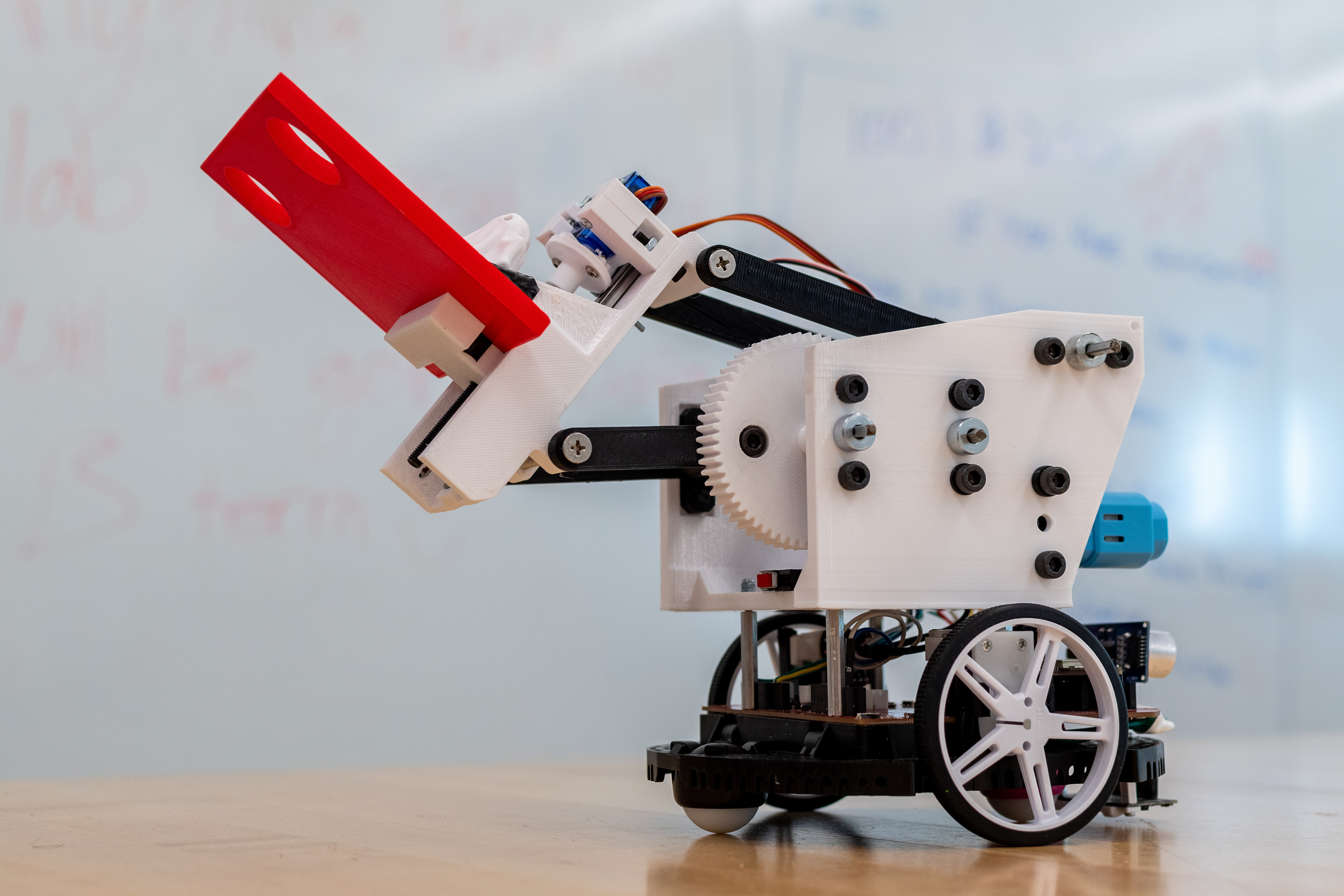
Linear Gripper Robot
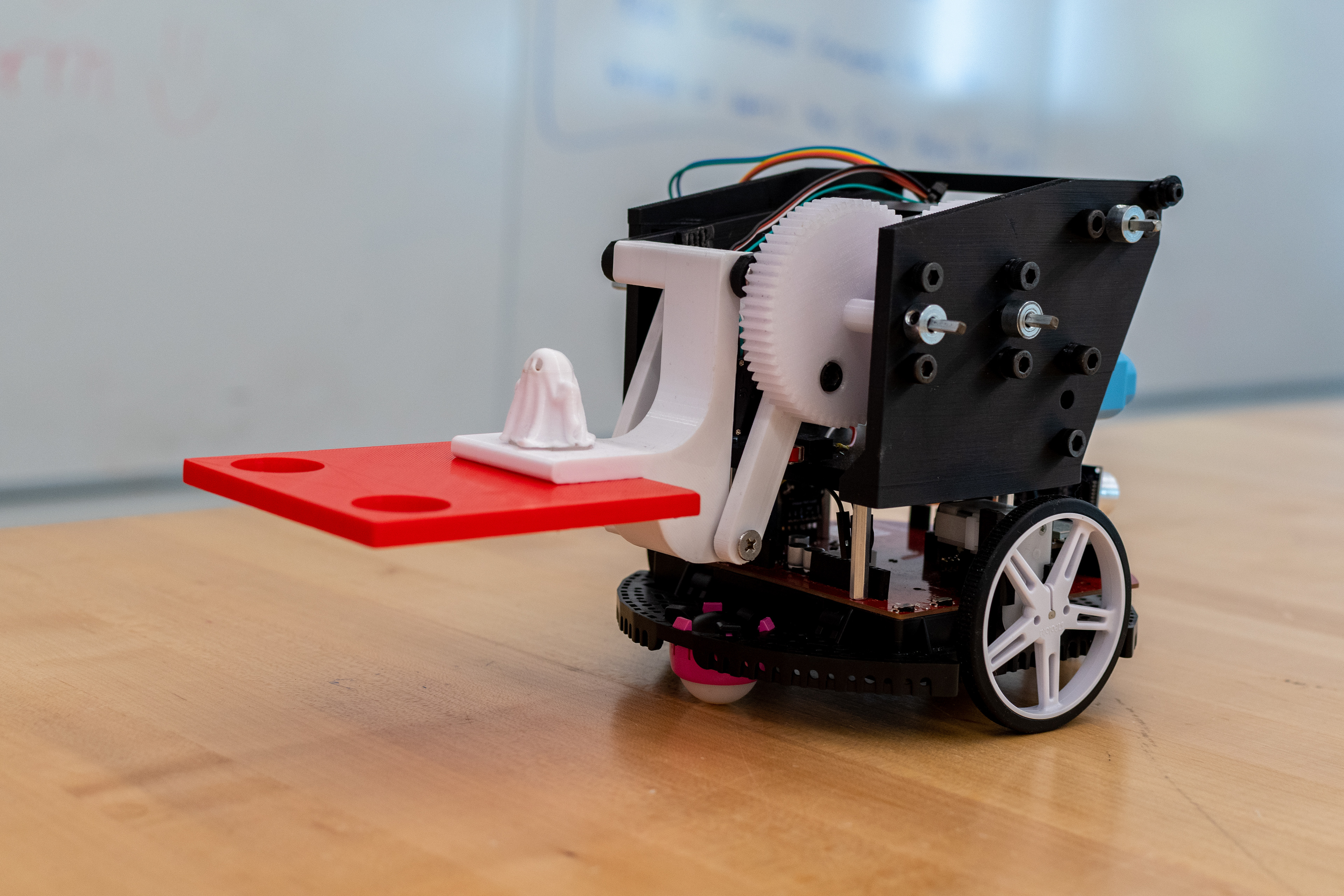
Bottom-out Gripper Robot
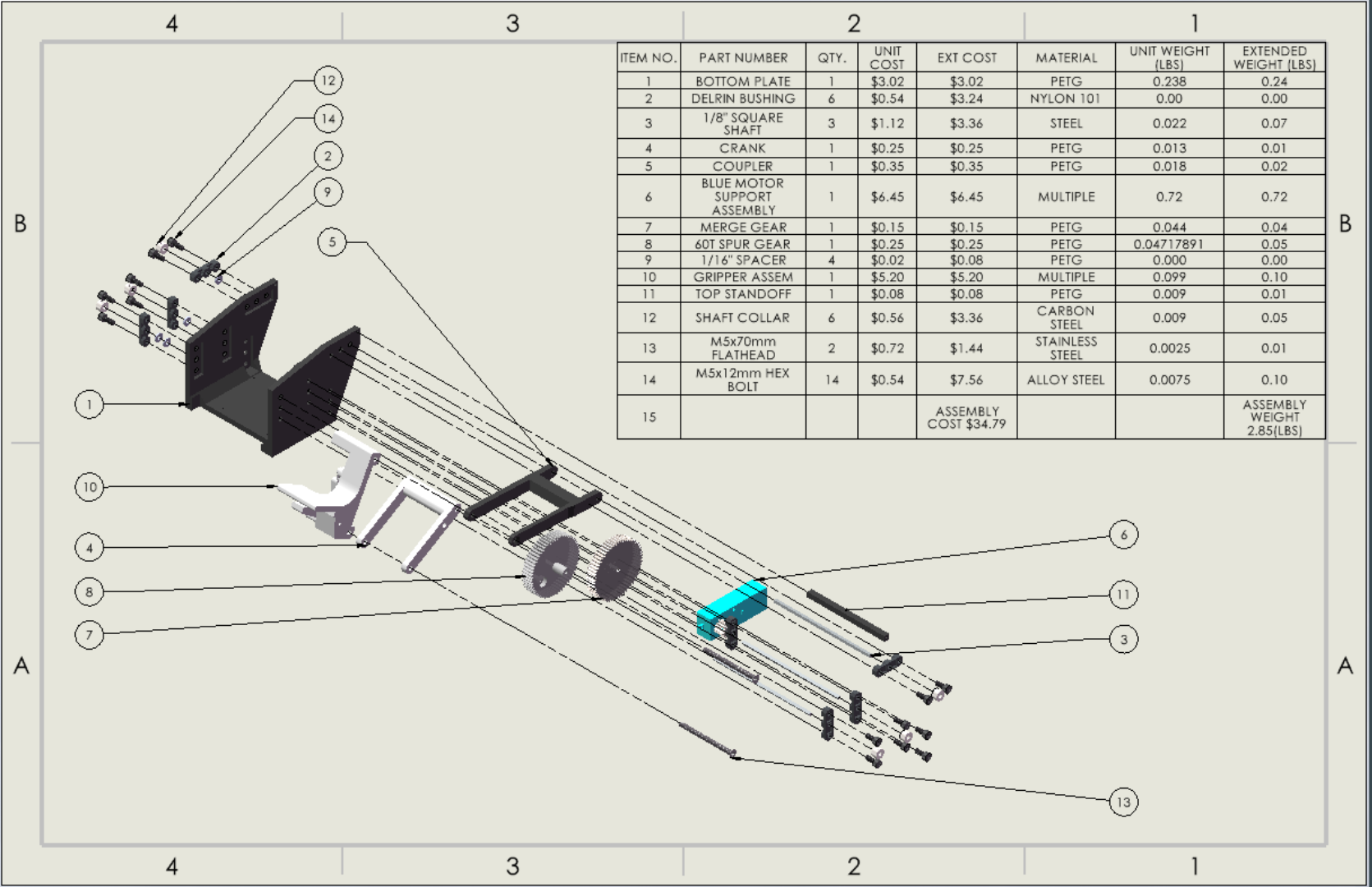
Bill of Materials and Exploded View of Arm
SolidWorks Demo of the Robot Placing Plate on a Roof Correctly
SolidWorks Demo of the Robot Placing Plate on a Roof Correctly
Video of the Final Demo, where one of the robots completes the entire course effectively: